数控机床的定位精度直接影响到机床的加工精度。传统上以步进电动机作驱动机构的机床,由于步进电动机的固有特性,使得机床的重复定位精度可以达到一个脉冲当量。但是,步进电动机的脉冲当量不可能很小,因而定位精度不高。伺服系统的脉冲当量可以比步进电动机系统小得多,但是,伺服系统的定位精度很难达到一个脉冲当量。由于CPU性能已有极大提高,故采用软件可以有效地提高定位精度。我们分析了常规控制算法导致伺服系统定位精度误差较大的原因,提出了分段线性减速并以开环方式精确定位的方法,实践中取得了很好的效果。
一、伺服系统定位误差形成原因与克服办法
通常情况下,伺服系统控制过程为:升速、恒速、减速和低速趋近定位点,整个过程都是位置闭环控制。减速和低速趋近定位点这两个过程,对伺服系统的定位精度有很重要的影响。
减速控制具体实现方法很多,常用的有指数规律加减速算法、直线规律加减速算法。指数规律加减速算法有较强的跟踪能力,但当速度较大时平稳性较差,一般适用在跟踪响应要求较高的切削加工中。直线规律加减速算法平稳性较好,适用在速度变化范围较大的快速定位方式中。
选择减速规律时,不仅要考虑平稳性,更重要的是考虑到停止时的定位精度。从理论上讲,只要减速点选得正确,指数规律和线性规律的减速都可以精确定位,但难点是减速点的确定。通常减速点的确定方法有:
(1)如果在起动和停止时采用相同的加减速规律,则可以根据升速过程的有关参数和对称性来确定减速点。
(2)根据进给速度、减速时间和减速的加速度等有关参数来计算减速点,在当今高速CPU十分普及的条件下,这对于CNC的伺服系统来说很容易实现,且比方法(1)灵活。
伺服控制时,由软件在每个采样周期判断:若剩余总进给量大于减速点所对应的剩余进给量,则该瞬时进给速度不变(等于给定值),否则,按一定规律减速。
理论上讲,剩余总进给量正好等于减速点所对应的剩余进给量时减速,并按预期的减速规律减速运行到定位点停止。但实际上,伺服系统正常运转时每个采样周期反馈的脉冲数是几个、十几个、几十个甚至更多,因而实际减速点并不与理论减速点重合。如图1所示,其最大误差等于减速前一个采样周期的脉冲数。若实际减速点提前,则按预期规律减速的速度降到很低时还未到达定位点,可能需要很长时间才能到达定位点。若实际减速点滞后于理论减速点,则到达定位点时速度还较高,影响定位精度和平稳性。为此,我们提出了分段线性减速方法。
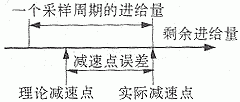
图1减速点误差示意图
在低速趋近定位点的过程中,设速度为V0(mm/s),伺服系统的脉冲当量为δ(μm),采样周期为τ(ms),则每个采样周期应反馈的脉冲数为:N0=V0τ/δ。由于实际反馈的脉冲数是个整数,可能有一个脉冲的误差,即此时速度检测误差最大值为l/N0=δ/(V0τ)。采样周期越小、速度越低,则速度检测误差越大。为了满足定位精度是一个脉冲的要求,应使V0很小,使得N0≤1,此时速度检测误差达到100%甚至更高。如果此时仍然实行位置闭环控制,必然造成极大的速度波动,严重影响伺服机构的精确定位。所以,我们认为此时应采取位置开环控制,以避免速度波动。
二、分段线性减速精确定位
1、方法与步骤
分段线性减速的特点是减速点不需要精确确定,减速过程速度曲线如图2所示。首先讨论最不利情况,即由伺服系统的最高速度开始减速过程,具体的减速步骤是:
(1)初始速度VG经AB段以加速度a2降速到V2,在BC段以V2匀速运行T2个采样周期,用BC这个时间段来补偿减速点A的误差。A点最大误差是VG对应的一个采样周期的脉冲数NG=VGτ/δ,速度为V2时一个采样周期的脉冲数为N2=V2τ/δ,则只要保证T2≥NG/N2=VG/V2,就可以使BC时间段补偿减速点A点的误差。
(2)速度V2经CD段以加速度a1降速到V1,在DE段以V1匀速运行T1个采样周期,用DE这个时间段来补偿减速点C的误差。类似地,应保证T1≥V2/V1。由于速度V1较低,假设取V1=5mm/s,脉冲当量δ=1μm,采样周期τ=1ms,则单位采样周期应反馈的脉冲数为N1=5,速度检测误差最大可达20%。所以,从这段过程开始就可以采用开环控制,以避免由于速度检测误差而引起速度波动。值得注意的是,开环控制算法应包括伺服机构的死区补偿和零漂补偿模块。
(3)速度V1经EF段以加速度a1降速到V0,在FG段以V0匀速运行T0个采样周期,直到到达定位点,这个过程采用位置开环控制。
通常情况下开始减速时伺服系统的速度(假设为VG1)小于最高速度,这时相当于减速起始点A向下移动到A1点,如图2虚线所示。如果初始速度小于V2,如图2中的VG2所示,相当于减速起始点移到了CD段,少了一段减速过程。

图2减速过程速度曲线
程序框图如图3所示,图中R为总剩余进给量(脉冲数),RA、RB、RC、RD、RE、RF分别对应图2减速曲线A、B、C、D、E、F点所对应的剩余进给量(脉冲数),可以由V、a、T、τ等参数算出。例如:

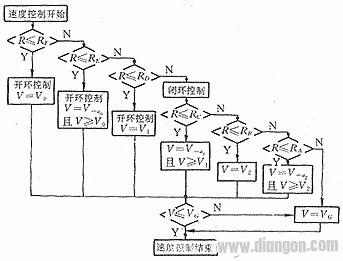
图3速度控制框图
2、几组参数的确定原则
(1)V0、V1和V2在常规的减速过程中,减速点的位置误差全靠最后低速趋近阶段来补偿,这样,V0就很不好选取。如果V0选得过小,应保证T0≥(VG/V0),则需要很长时间才能到达定位点;如果V0选得较大,直接影响定位精度。分段线性减速方法与常规的减速方法相比,增加了BC、DE两个时间段,减速点的位置误差可以在较高速度得到绝大部分的补偿。因此,V0可以选得很小。通常可取伺服系统的最低速度,这样可以提高伺服系统的定位精度。V1、V2可分别取伺服系统最高速度的1%和10%。
(2)a1、a1和a2 加速度越大,减速过程越短,但引起的冲击和误差也越大。因此,在高速阶段加速度可取大些,以保证减速过程的快速性;低速阶段应取较小的加速度,以保证定位精度。通常a1的值在数值上可取为与V0相等。
(3)T0、T1和T2 由前面分析可知,为了补偿减速点的位置误差,应取T0=KV1/V0,T1=KV2/V1,T2=KVG/V2,式中K为可靠性系数,用来补偿算法的计算误差及其它一些不确定因素的影响,常取K=1.1~1.3。
该方法与伺服系统本身特性无关,可作为任何伺服系统在任意速度下减速控制方法。在我们为上海机床厂研制的YKA7232蜗杆砂轮磨齿机数控系统中,采用了分段线性减速开环趋近定位点的控制方法。实测各轴定位精度和重复定位精度都控制在一个脉冲当量内,性能稳定,获得了很好的效果。